In the process of making or purchasing a garment bag, it's easy to overlook a small but vital detail-the zipper. As a key component to connect the opening of the garment bag, a high-quality zipper can not only ensure the practicality and durability of the product, but also convey the brand's taste and attitude through a unique design language.
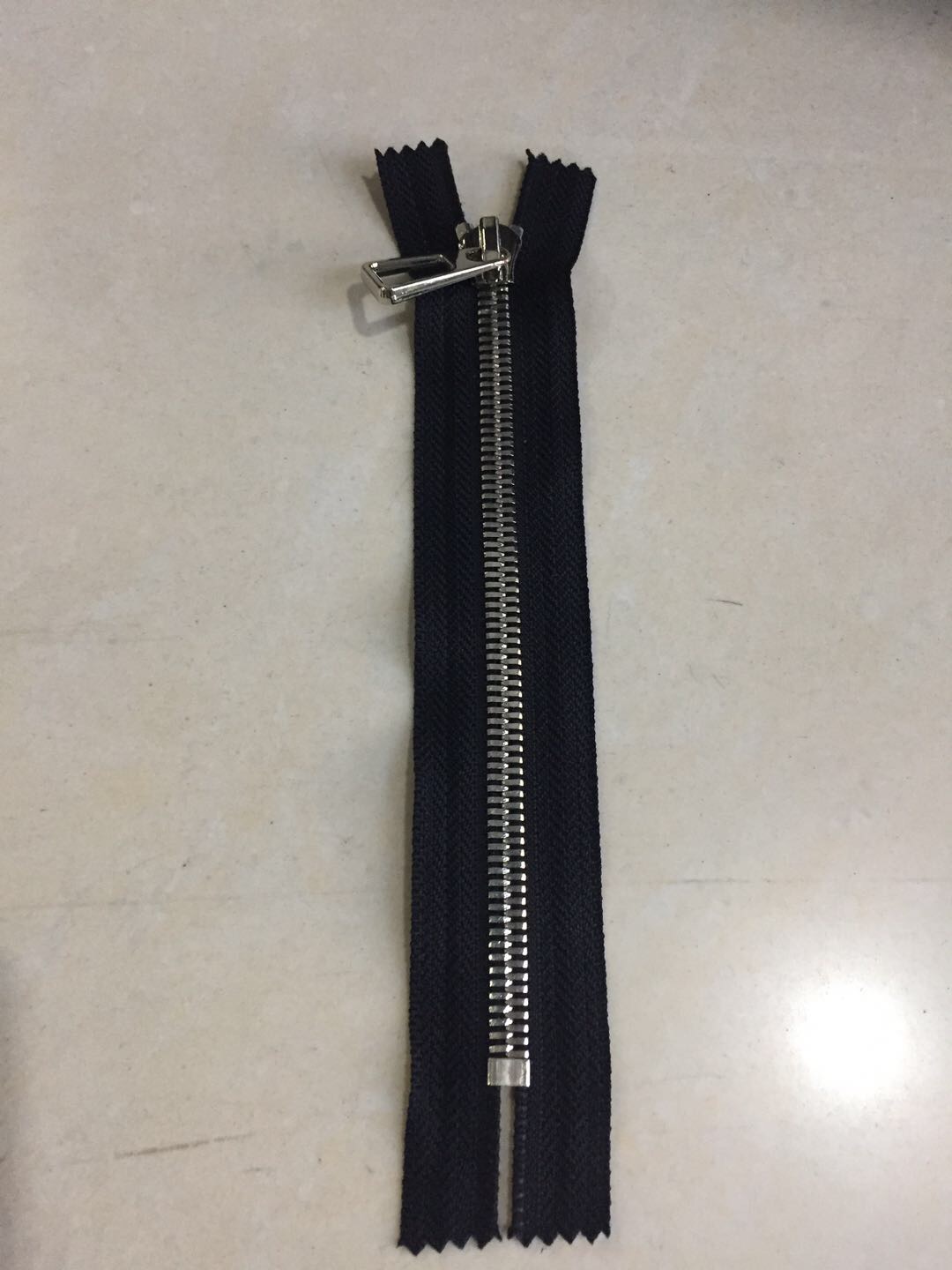
Whether it's a high-end custom gift box or a storage bag for daily use, a high-performance and elegant-looking zipper can make the overall texture leap onto the paper. Therefore, when choosing a zipper, it is necessary to take into account both functional and aesthetic requirements.
For designers, deciding which material to use is often the first and most important step. At present, there are two main types on the market: metal pull head is known for its sturdiness and wear resistance; while plastic pull head is popular because of its light and environmentally friendly characteristics.
Both have advantages and disadvantages, depending on the actual application scenario and personal preference. If the pursuit of luxury and budget allows, you can choose the surface after special treatment (such as chrome plating) after the metal products; and for customers who focus on sustainable development, the plastic version made of recyclable materials is clearly a better option.
Compared with the traditional ordering mode, "in stock direct supply" undoubtedly brings more convenient conditions for enterprises. "Time is money", especially in a highly competitive market environment. In this way, you can quickly obtain the required quantity of products, timely meet orders and reduce inventory pressure.
In addition, prices are more competitive due to the removal of middlemen. This means that you can get the same quality or even higher-grade goods at a lower cost, thereby increasing your profit margin.
then the question arises: what kind of production process can ensure that every zipper delivered to customers has stable and consistent quality? the answer is very simple, but it is not easy to implement-that is, to adhere to high standards and strict requirements throughout the whole manufacturing cycle!
The first is a strict screening and auditing mechanism for raw material suppliers. Only goods that meet the specified standard specifications will be accepted into storage. Secondly, in the processing stage, the method of combining advanced equipment with manual detection is used to check whether each process step is accurate and in place. Finally, it is necessary to organize regular staff training to learn the latest technology and operating specifications in order to continuously improve the overall ability and quality of the team.
Many well-known brands have long been aware of this and regard it as one of the important components of building a good public image. For example, a well-known sneaker manufacturer has adopted a special customized version of the invisible magnetic suction closure system provided by our company instead of the ordinary style on the packaging of its new series of products, which not only improves the user's unpacking experience but also indirectly promotes the growth of the willingness to repurchase.
another example is a retailer specializing in children's toys, which received a large number of positive feedback from parents and consumers after replacing it with a new type of safety head with a protective cover design, praising it as very considerate and taking into account the potential risk factors in children's play and avoiding unnecessary troubles.
Of course, facing a wide variety of styles and models will inevitably make people feel confused and confused. I don't know how to start. Don't worry, please remember the following simple and easy to remember tips to help you find the best partner for your project characteristics faster:
as long as the final decision is made after checking and confirming one by one according to the above tips, there will not be too much deviation ~